G.J. Gardner Homes setting new standards
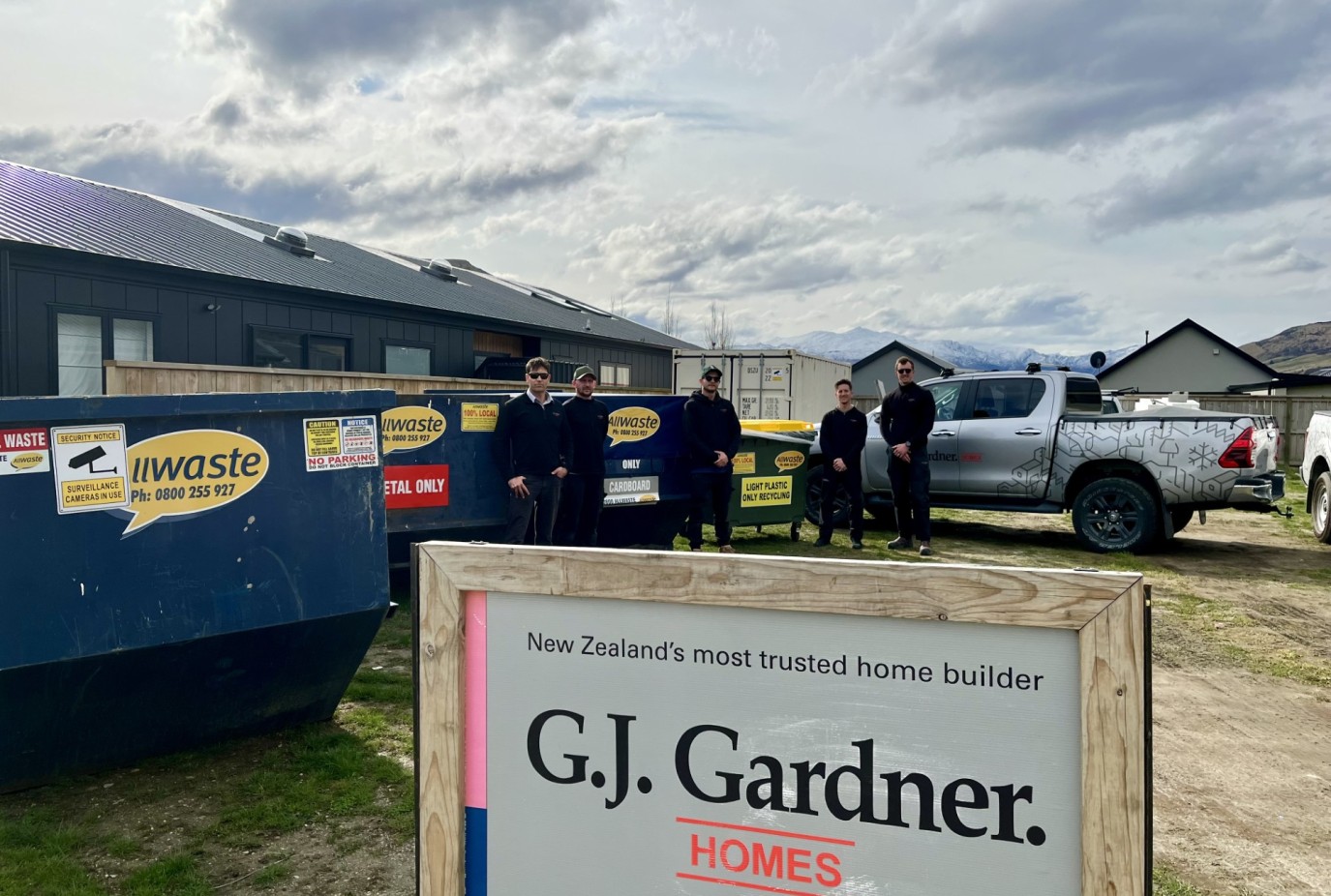
Five tonnes of GIB board, at least a couple of tonnes of metal, 400kgs of cardboard, and as much left over plastic as possible.
That’s what G.J. Gardner Homes Queenstown Lakes centralised Hanley Farm recycling depot is diverting from landfill each month.
The local franchise of New Zealand’s most-trusted house building company struck on the smart idea of using one vacant section as a place to gather all recyclables while working in the subdivision, where it has up to 40 homes under construction at any one time.
Following the success of this, GJ Gardner have set up a similar recycling site for their builds in Wānaka and Hāwea.
And GJ’s Queenstown Lakes GM Stephen Hardy says it’s almost cost-neutral because the metal can be sold on.
“The younger generation coming through are now really, really passionate about sustainability, it’s very important to them as it is to us,” he says.
“So this project is client-driven, but what has blown me away is the appreciation from the trades as well, for the steps we’ve been taking. I’ve actually got emails of thanks from some tradies, particularly electricians, who said they were gutted to be throwing away the cardboards and plastics, and had previously tried to recycle them but it proved too challenging logistically.”
Hardy says recycling on a section-by-section basis is hard, because there’s not much space for the different bins and tradies need to add in trips to the recycling depot. It can even be a challenge to get a skip on some of the sites.
The company already reused some elements, like all its plastic wraps, but has been working with All Waste to ensure as much of its construction waste is recycled as it can.
“For the GIB board, it’s the off cuts but an astronomical amount really, five tonnes per month on average and some months up to eight tonnes. It can be turned back into landscaping products. The cardboard is around 400kgs per month and the metal fluctuates.”
The communal depot has worked so well, Queenstown Lakes District Council has taken an interest in using it as a case study, while Hardy’s also had discussions with Wānaka’s Better Building Working Group, formed from the 2018 Wao Summit. The group has 40 members, including GJs.
“It’s something we contribute a lot of volunteer time toward for the greater good. It’s about sharing the knowledge for better standards,” Hardy says. “I definitely think we’re leading the way and setting a new standard in Queenstown. But for us, it’s a bit of future-proofing, because I’d anticipate down the track, either through the building code or consenting through council, this level of recycling will become mandatory.”
G.J. Gardner Homes is also looking to tackle the problem earlier in the supply chain, offering customers the option to build more sustainable homes.
“We’ve been working with suppliers on a local and national level to identify sustainable products and next month [October] we’re rolling out a sustainable specification for our clients, that they can choose as standard for their build.
“It will include wool insulation, wool carpets, recycled underlays, plant-based paints, renewable timber claddings, that sort of thing.”
With construction, the company already uses 140mm framing as standard, allowing for better insultation, which in turn means using less energy to heat the house. It also offers energy efficient windows and on a national level partners with Harrison Solar.
“We offer some really good deals with national buying power for our clients there, and with advancements in battery technology, we’re seeing more and more clients request solar. There are also some good deals out there from the energy companies for discounted or free energy in the evenings for households with solar, with the offset being that the feed into the grid in the daytime, so that’s making it more popular.”
For more information about G.J. Gardner Homes Queenstown visit www.gjgardner.co.nz or ph. 0800 42 45 46